LEM, The ultimate gasket
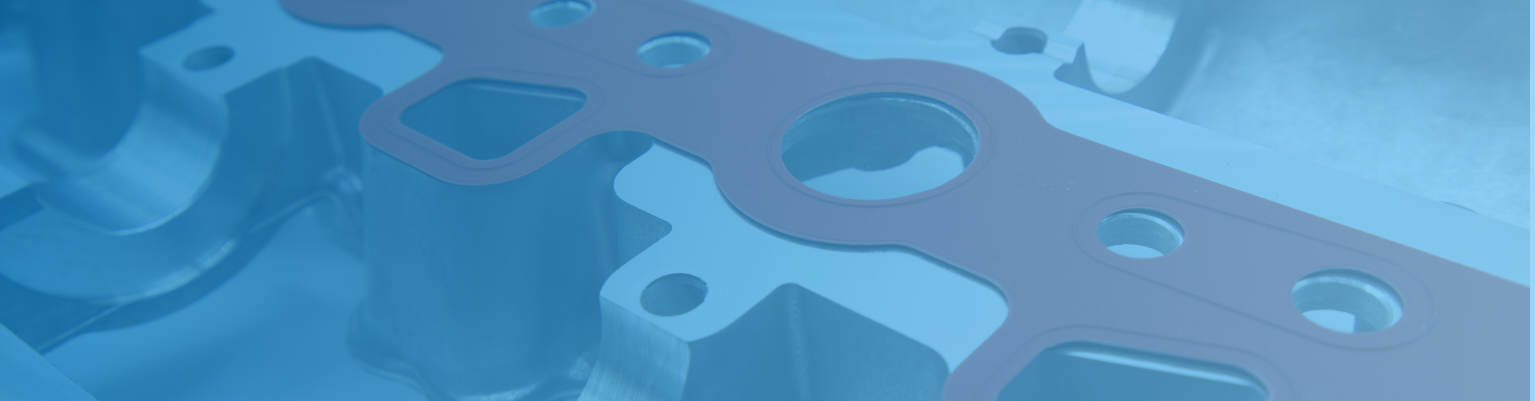
What is LEM
The manufacturing process of our LEM technology consists of a rigid carrier on which we over mold liquid silicone elastomer. The rigid carrier is currently made of zinc coated steel, stainless steel or aluminium. During the moulding process, we shape the beads of silicone according to the specific design pattern, result of your parts’ design and their deformation with environmental conditions.
The silicone liquid elastomer is the perfect material to increase your process capabilities due to its fast curation properties enhancing gains of time in productivity.
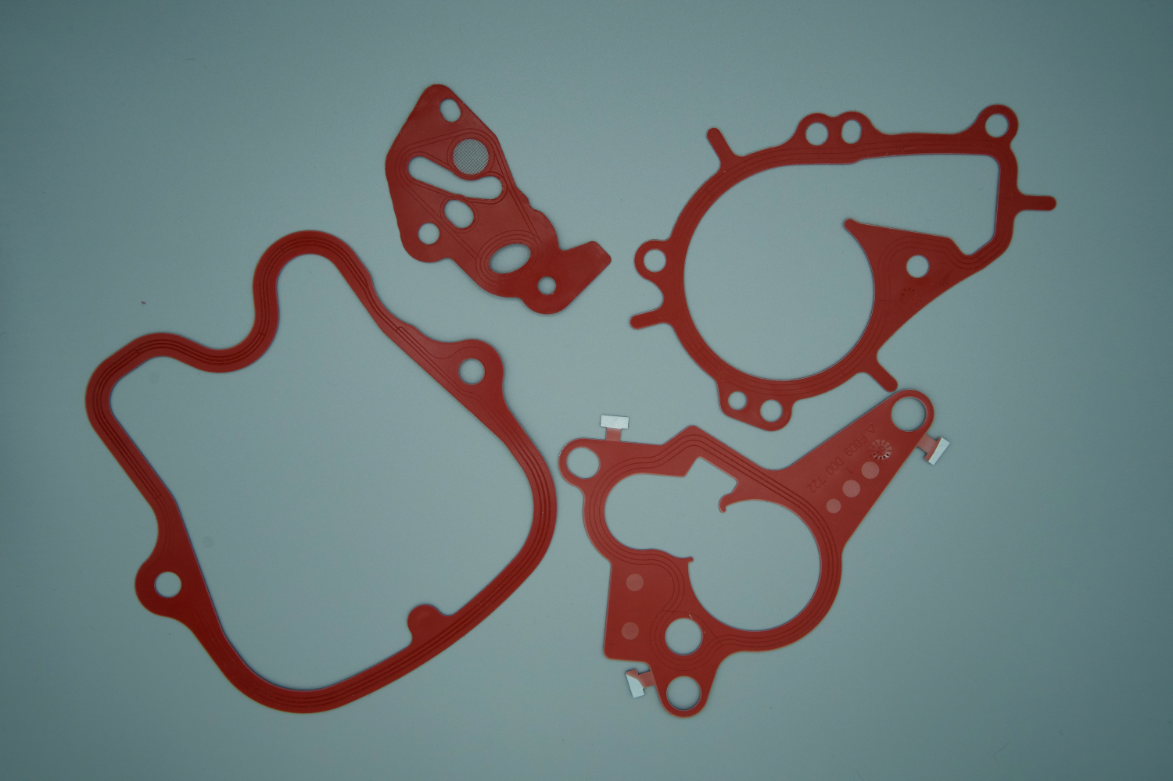
What makes our sealing technology so innovative is the elastomer’s singular design. We place several sealing beads in parallel to one another multiplying the number of barriers upholding the fluids, to integrate the best possible sealing robustness to your system. Furthermore, due to the topography of the sealing beads present on our LEM gaskets, they are adaptable and compatible to any type of design required to fit your housing and cover systems. Depending on the profile of the parts to be sealed, we will accordingly adjust the topography of the cord’s range to your needs; so that our gaskets seal properly and apply even pressure overall the parts, resulting in additional robustness and an extended lifetime of your systems.
Our tailor made LEM gaskets have been primarily designed and manufactured for combustion engines within the automotive, industrial, truck, agricultural and heavy machinery markets and many more.
For the last 10 years we have been growing our knowhow in the conception of next generation LEM gaskets made adaptable to new markets segments. Since then we have been investing in the emerging E-mobility technologies within the E-bikes, fuels cells and hydrogen powered systems.
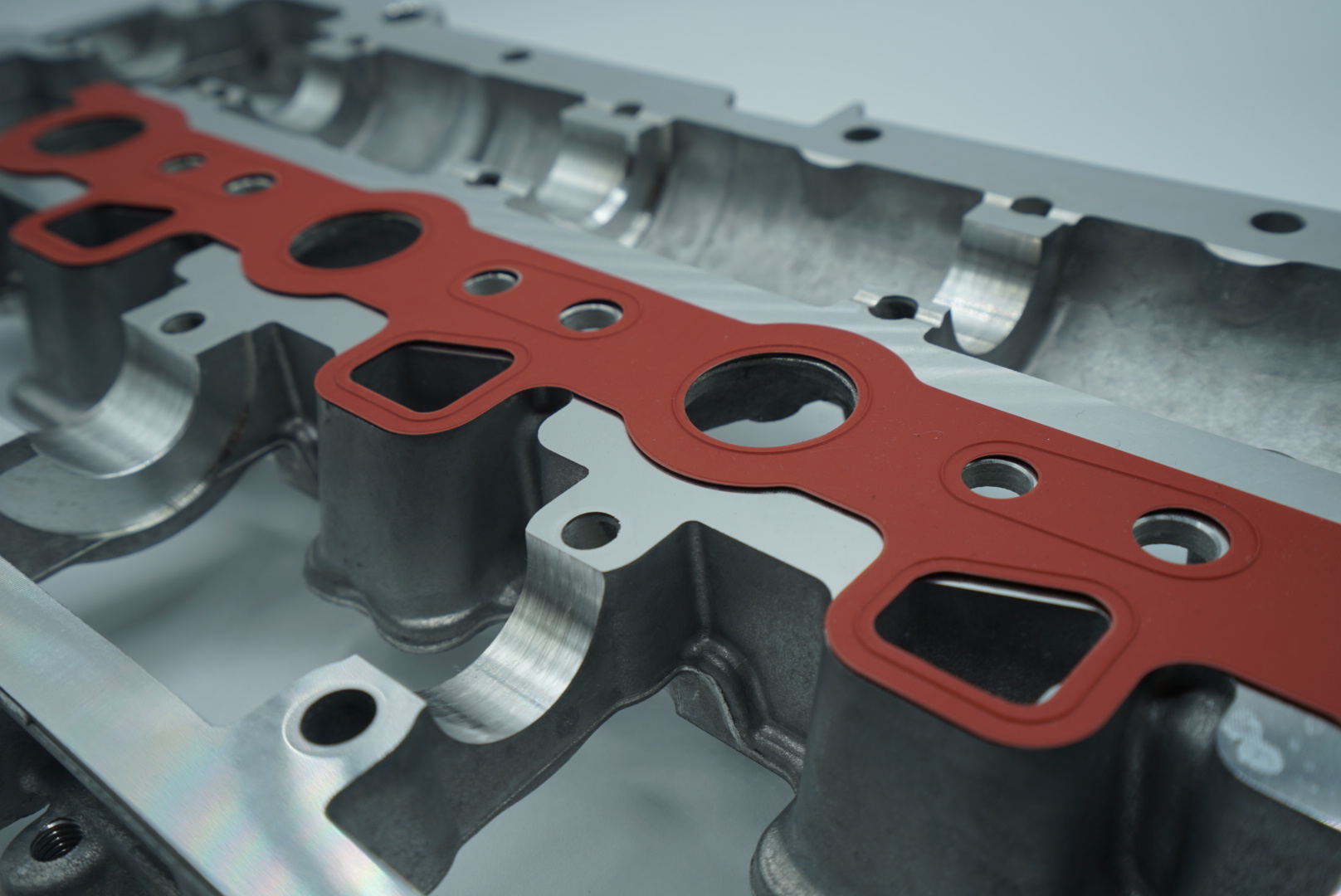
Our LEM technology is an adaptable material which allows multiple functions to be added on to your gaskets. The implementation of filtration systems, conductivity, T-junctions and more are possible due to the multifunctional nature of our technology.
With our process, we can manufacture gaskets up to 750mm by 450mm wide but if in need of a bigger gasket, puzzle assembly is conceivable.
Let’s discuss your needs and find the perfect sealing solution suited for you.
LEM Design - project management
Our LEM technology’s key attribute is its topographic pattern. It allows the adjustment of the distance between the bolts and any deformations of the housing system subject to mechanical stress. Here are the steps we follow to ensure an exact dimensioning of the topographic sealing beads:
1. Analysis & Adaptation
We perform an analysis of your system, so that the LEM technology will adapt perfectly to your housing and cover. The most Important geometrical parameters are: material type, thickness, width and rigidity of the parts. We also consider your boundary conditions: mechanical forces, temperature, distance between screws, deformations and fluid to be sealed.
For applications involving air, coolant water and oil, our red or black silicon are well suited.
For hydrogen applications, we recommend our blue dedicated silicon.
Depending on the material of your housing and cover, we adapt the carrier of the LEM gasket by using zinc coated steel, stainless steel or aluminium. Our engineering team designs our gasket’s geometry directly from your 3D model. Then, they adapt the height of the sealing beads in order to compensate for the distance between bolts and deformation of the flanges based on our standards and 20 years of experience.
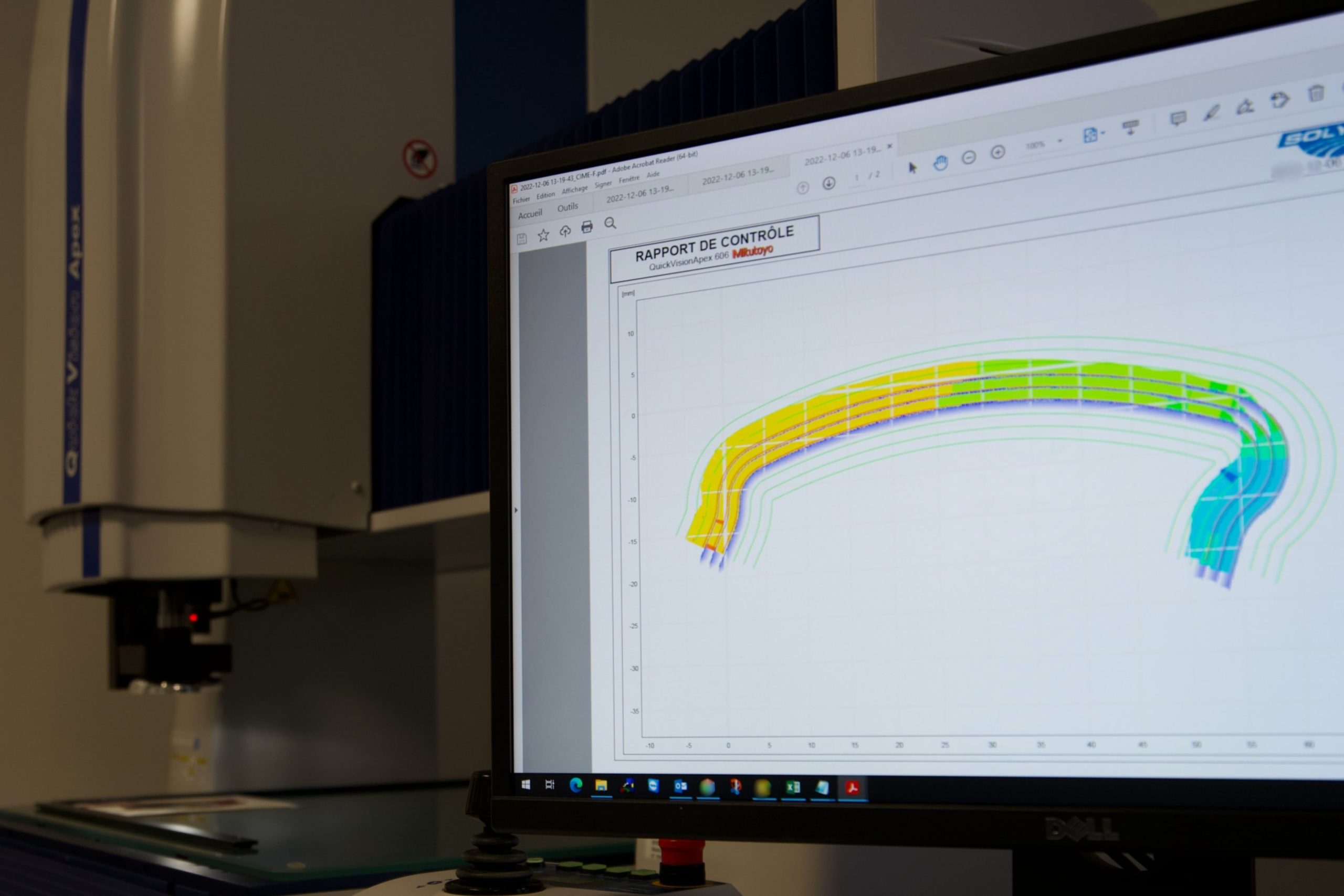
2.Prototyping & control
After the design freeze of the LEM gasket, the prototyped parts will be ready and delivered in only 8 weeks. The samples are nearly representative to the serial parts:
- During the production of the LEM prototypes, the parts are molded and laser cut, whereas serial parts are molded and stamped for a better productivity.
- Carrier and elastomer materials are the same for samples as for serial parts.
After production of the LEM prototypes, we control the aspect of the gaskets. We measure their geometry according to the drawing. We test their functionality with FUJI paper to ensure that geometry fits the requirements and that contact pressure between the gasket and housing is enough to avoid any leakage during the lifetime of the product.
Solyem is an experienced and reactive company. After validation of the prototypes, our standard lead-times are:
- 16 weeks for off-tool parts delivery
- 18 weeks for PPAP delivery
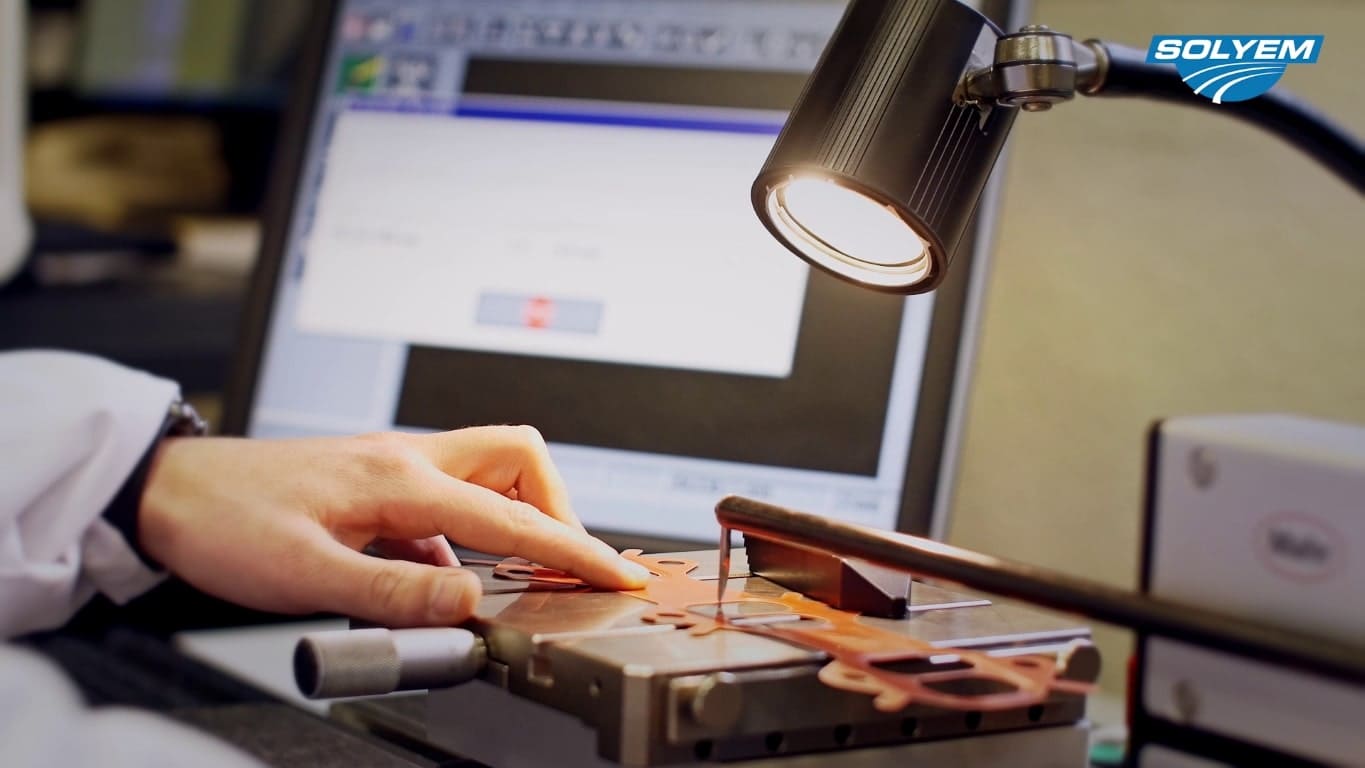
Contact
34 chemin Pierre Blanche
69800 SAINT-PRIEST
France
Switchboard: +33 4 72 23 25 25
Human Resources: +33 4 72 23 25 01
Sales: +33 4 72 23 24 57
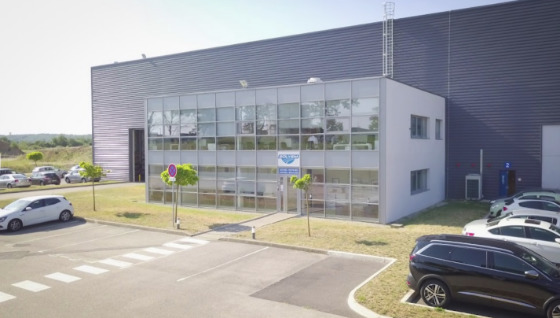