News
What is static sealing ?
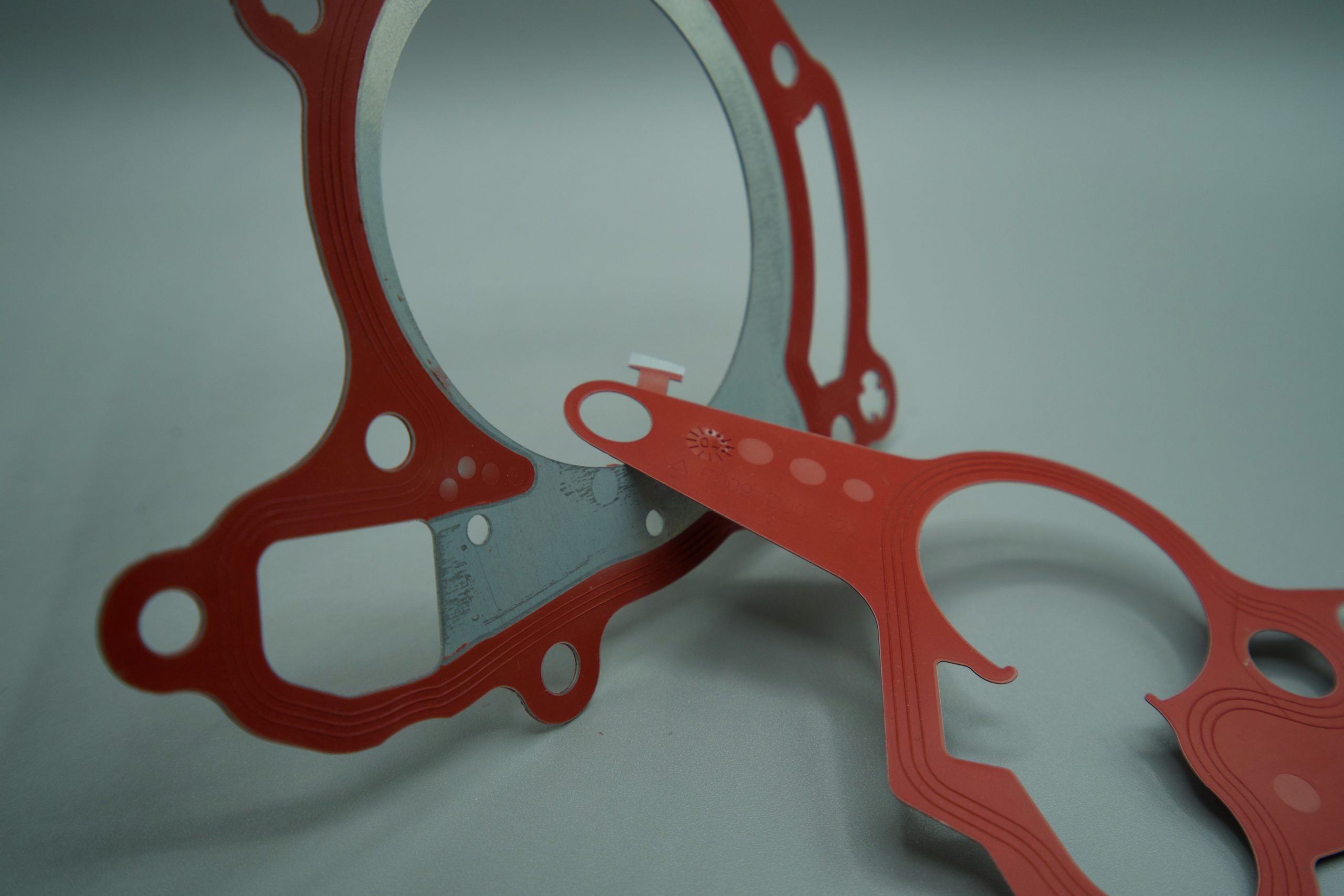
When using various equipment, precautions must be taken to prevent the entry of external contaminants, as well as the leakage of gases, liquids and solid particles through the interfaces. Stability and durability of the seal for the lifetime of the equipment is therefore essential, but often forgotten.
Static sealing is widely used in mechanical and electrical equipment. One direct measure of sealing is the leakage rate. In static sealing, leakage between two sealing faces, known as interface leakage, is the main cause of seal failure. These leaks are strongly affected by the ageing of the sealing materials. Interface leakage often occurs when the two apparently contacting surfaces have macroscopic and microscopic roughness such that contact is not made perfectly between the surfaces, creating leakage paths.
In order to reduce the leakage rate, the leakage paths must be blocked to prevent the fluid from passing through and thus improving the static sealing of the equipment. Therefore, it is recommended to reduce the surface roughness and increase the effective contact area between the interfaces in order to reduce the number of leakage paths and thus improve the static sealing. For this reason, elastomeric materials are widely used because of their excellent performance in these fields.
The overall quality of your assembly depends on your ability to choose the right partner for your sealing conditions to design the perfect static sealing solution.
A common mistake in managing the development of new equipment is to assume that, because the gasket is a small, low-cost part compared to other parts of the assembly, it should be considered at a late stage of development. Your sealing partner is a very important member of your project, and the best way to make your project a success is to involve them as early as possible, so that together we can define solutions, which will best fit your boundary conditions. Your sealing partner can then bring all his knowledge and experience to bear on optimising the design of your housing parts and the shape of the seal, taking into account the temperature range of your application, the relative pressure in your system, the deformations of your housings and the medium to be sealed. Involving your sealing partner at an early stage will surely lead to productivity gains in the production of your parts as well as in the assembly of your equipment.
Do you want to improve the sealing of your system, but also improve the design of your housing parts and improve the productivity of your products and assembly lines by choosing the best sealing solution on the market ? Contact Solyem !
Other Posts
Contact
34 chemin Pierre Blanche
69800 SAINT-PRIEST
France
Switchboard: +33 4 72 23 25 25
Human Resources: +33 4 72 23 25 01
Sales: +33 4 72 23 24 57
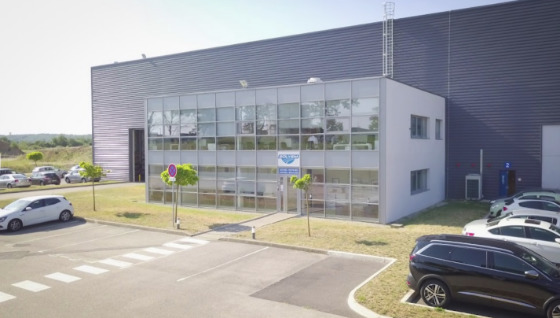